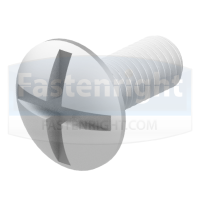
See Products
Aluminium Screws, Nuts & Bolts
Aluminium Fasteners are lighter and more malleable than stainless steel, with a high weight to strength ratio. They are often used in applications such as car manufacture, medical equipment and aerospace, where minimising weight is important.
They are also aesthetically pleasing and robust fasteners, with high corrosion resistance. Aluminium is not magnetic, so is ideal for use in electronics and sensitive applications.
Aluminum screws and fixings are available from stock, or on short lead times. See products below.
Most of our other fixings can be manufactured from aluminium, with options for special finishes. These are made to order, minimum quantities apply.
Make an enquiry about Aluminium Fasteners
Showing all 14 results
-
Aluminium Socket Head Cap Screws (DIN 912)
SKU: ALU01
-
Aluminium Hexagon Head Screws (DIN 933)
SKU: ALU02
-
Aluminium Socket Button Head Screws
SKU: ALU03
-
Aluminium Socket Countersunk Screws (DIN 7991)
SKU: ALU04
-
Aluminium Pozi Pan Head Screw (DIN 7985)
SKU: ALU05
-
Aluminium Hexagon Full Nuts (DIN 934)
SKU: ALU06
-
Aluminium Nyloc Nuts (DIN 985)
SKU: ALU07
-
Aluminium Flat Washers
SKU: ALU08
-
Aluminium Spring Washers
SKU: ALU09
-
Aluminium Slotted Roofing Bolts
SKU: ALU10
-
Aluminium Pozi Countersunk Head Screws (DIN 965)
SKU: ALU11
-
Aluminium Slotted Grub Screw Flat Point (DIN 551)
SKU: ALU12
-
TX Aluminium Micro Profile Head Screws
SKU: MPH04
-
TX Aluminium Coloured Micro Profile Head Screws
SKU: MPH05
Aluminium and its use in Bolts, Screws, Nuts and Washers
What is Auminium?
Aluminium is a silvery white metal that is very soft in its pure form, making it unusable for many purposes. When combined with other elements such as silicon, copper, iron, manganese, and magnesium, this creates an aluminium alloy which increases tensile strength and supplies other useful qualities.
This metal is often demanded for high-performance applications that require an extremely lightweight material, as well as one that is highly durable and hosts good corrosion resistance. Aluminium is also an attractive metal, providing an aesthetic appearance to any environment where it is deployed.
Advantages of Aluminium Fasteners
The most desirable property of aluminium bolts, screws, nuts & washers is their low density. Aluminium is 2.5x less dense than steel and approximately 66% less dense than titanium. In fact, it is one of the lightest materials used for engineering, with a strength-to-weight ratio greater than both steel and stainless steel. Although these fasteners may not be as strong, the correct grade can provide a range of advantages to many applications.
Another benefit of aluminium fasteners is their strong resistance to various forms of corrosive media. When placed in certain substances and environments, a thin passivation layer is formed on the surface of the material. This provides additional protection against concentrated nitric, sulfuric, and organic acids, as well as general atmospheric corrosion. In addition, fasteners made of aluminium are not known to rust over time.
Aluminium is also non-magnetic and an excellent conductor of both electricity and heat. Apart from copper, it is the most used material for a wide range of conductors due to its overall cost and availability. In comparison, aluminium parts are up to twice as conductive by weight than those made of copper, making them an ideal choice if the weight of a component also needs to be considered.
Common Applications for Aluminium Fasteners
With their unique set of properties, aluminium bolts, screws, nuts & washers find use in an extensive range of general and specialised applications. Many building and construction projects rely on aluminium for its lightweight nature and corrosion resistance. The same can be said for industrial machinery and equipment, where good mechanical strength is imperative to ensure safety and smooth operation of hardware.
Electrical applications tend to favour materials such as aluminium because it is highly conductive, does not rust, and is relatively cost-effective. It can be found in medical environments and is typically considered much safer than equipment made of plastic or stainless steel due to its non-toxic properties. Automotive manufacture also sees aluminium fasteners demanded for their low weight and durability.
One of the more specialist uses of aluminium bolts, screws, nuts & washers is in the aerospace and aeronautical sector. These fasteners are found on most types of modern aircraft and spacecraft – often to join structural components. This is primarily due to the high strength-to-weight-to-cost ratio which enables a plane to carry larger loads while helping to increase fuel efficiency.
When to Avoid Aluminium
While aluminium components are perfect for many situations, they will be less effective for others. This includes high temperature applications due to aluminium’s relatively low melting point of between 450°C and 670°C. In addition, aluminium generally performs better at reduced temperatures where its tensile strength is improved, unlike metals such as steel which become brittle. If a fastener is required for high temperature service, materials such as inconel or molybdenum could be more suitable.
In many cases, the application may demand a material with high tensile strength. Although aluminium fasteners are extremely lightweight and boast an impressive strength-to-weight ratio, they are relatively ductile and struggle to support heavier workloads. If a stronger fastener is essential, then opting for a material such as stainless steel may be more beneficial. If strength and weight both need to be considered, then titanium might be the material for you.
Aluminium bolts, screws, nuts & washers are resistant to many forms of corrosive media, however there are some limitations to this. Galvanic corrosion is one of the most common types of corrosion in aluminium. As it is one of the least noble metals and highly reactive, corrosion can occur when these fasteners come into contact with more noble metals such as carbon steel. They are also prone to corrosion by dilute acids, alkalis, and chlorides.
Choosing the Correct Grade
There are hundreds of different aluminium alloys that exist, each with their own unique properties and uses. They are classified into eight series of grades, where each grade also has an associated temper. The temper designation, often denoted by the letter T or H, defines how the alloy was treated during the manufacturing process – either with or without heat. This reflects many of its physical properties.
It is important to know exactly which grade and temper you require when looking to purchase aluminium bolts, screws, nuts, washers & fasteners, as this will have an impact on both price and performance.
There are two series which are most utilised in the manufacture of aluminium fasteners.
6000 Series
Known as the general-purpose series, the aluminium 6000 series is primarily alloyed with silicon and magnesium. These grades find use across a wide range of applications and industries, hosting good strength and corrosion resistance.
Grade 6061
One of the most common alloys in the series and is often referred to as the “workhorse” grade, sharing many similarities to grade 6082. In fact, they are considered near equivalent due to their almost identical chemical composition. For this grade, aluminium 6061-T4 and 6061-T6 are the most common tempers.
Grade 6063
Another common alloy which typically has greater corrosion resistance and a better surface finish compared to 6061. It features a slightly higher melting temperature, as well as better thermal conductivity. Similar to 6061, aluminium 6063-T4 and 6063-T6 are the most common tempers.
7000 Series
The aluminium 7000 series include the addition of zinc as its major alloying element, usually with fair quantities of magnesium and copper. This promotes high strength and hardness as the standout properties which can also be observed at elevated temperatures.
Grade 7075
By far the most common alloy in the series for aluminium bolts, screws, nuts & washers. It hosts strength levels higher than many grades of mild steel, so is widely used when a strong but lightweight material is required. However due to their slightly different composition, 7000 series grades do not have the same corrosion resistance as those in the 6000 series. Aluminium 7075-T6 is the most common temper for this grade.
Aluminium Bolts, Screws, Nuts & Washers Available Now
Here at Fastenright we supply a wide range of aluminium fasteners, many of which are supplied from stock or are available to order with relatively short lead times. While the most common grades are discussed above, other grades and tempers of aluminium can also be provided. You can browse our range at the top of this page. We specialise in non-standard fasteners, therefore we can supply non-standard sizes, grades, and finishes, as well as bespoke components made to customer drawings. These are all subject to minimum order quantities.